Lautsprecher-Ständer selber zu bauen, ist aus verschiedenen Gründen keine schlechte Idee.
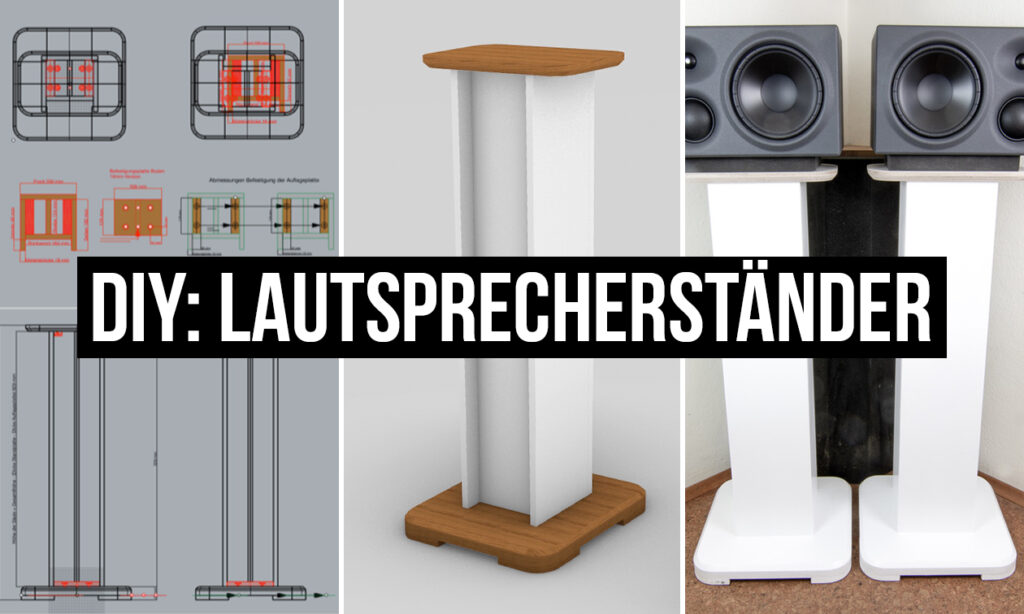
Diese Anleitung hilft, Monitor-Stative nach eigenen Wünschen selbst herzustellen! Es beruhigt es ungemein, wenn die schweren und teuren Abhörmonitore auf ausreichend stabilen Ständer stehen und von der Höhe und der Haptik genau passend sind. Was gute Stative bringen und warum Selbstbau eine gute Option ist, behandelt dieser Artikel auch – in erster Linie aber den kompletten Bau von der Planung bis zum fertigen Boxenständer-Paar.
- DIY-LAUTSPRECHERSTATIVE: WOZU?
- DIY-LAUTSPRECHERSTÄNDER: PLANUNG
- Anforderungen an die Selbstbau-Stative
- Schritt 1: Höhe bestimmen
- Schritt 2: Die 5-Minuten-Konstruktion
- SELBSTBAU-STATIVE: BAUPHASE
- Schritt 3: Das Material besorgen
- Schritt 4: Verleimen der Bodenplatten
- Schritt 5: Herstellung der Befestigungsstücke
- Schritt 6: Verleimen der MDF-Säule
- Schritt 7: Schöner machen!
- Schritt 8: Grundieren und Lackieren
- Schritt 9: Das Befüllen mit Quarzsand
DIY-LAUTSPRECHERSTATIVE: WOZU?
Spielt ein Stativ akustisch eine Rolle?
Eine schwierige Frage: Hat es eine akustische Auswirkung, auf was die Monitorboxen stehen? Gerade in HiFi-Kreisen wird das kontrovers diskutiert, aber so richtig handfeste Untersuchungen mit entsprechenden Messungen sind zu diesem Thema schwer zu finden. Ich wage mal die Behauptung: In einem akustisch unbehandelten Raum ist Rolle des Boxen-Stativs eher zu vernachlässigen. In einem akustisch behandelten Raum kann ein wackeliges Stativ, das mitschwingt oder Schwingungen an die Umgebung überträgt, aber durchaus den Sound am Abhörplatz deutlich negativ beeinflussen. Bei mir war das der Fall, deswegen musste schnellstens neue Boxenstative her!
Meine Ausgangslage
Für meine Boxen Neumann KH 310 A war ich auf der Suche nach stabilen Lautsprecherstativen. Jede Box wiegt immerhin 13 kg und das liegende Dreiwege-System passte nicht so recht auf die vorhandenen Säulenstative aus Metall. Zum einen war das eine wackelige Angelegenheit, zum anderen vibrierte das Stativ bei basslastigen Tracks mit.
Was es zu kaufen gibt und warum sich DIY lohnt
Eine kleine Marktanalyse später war ich nur bedingt schlauer, angeboten werden im Prinzip zwei Typen von Lautsprecher-Stativen/Ständern: Metallstative, bei denen die tragende Säule aus einem (oder mehreren) Metallrohren bestehen, oder Ständer aus Holz- oder Plattenmaterialien mit einer rechteckigen tragenden Säule aus vier Holzplatten. Alles was mich optisch und funktional ansprach, war leider mit einem entsprechenden Preisschild versehen, sehr schnell war deshalb mein DIY-Ehrgeiz geweckt: Vier Platten zusammenschrauben und einen Deckel und Boden dranpappen? Das schaffe ich auch! Dachte ich… Spoiler: So einfach war es dann doch nicht.
Die Höhenproblematik
Für die ideale Abhörsituation muss die Box auf einer genau definierten Höhe stehen. Diese Höhe ist abhängig von der Bauart der Box, dem Aufbau eures Studios/Arbeitsplatzes. Damit haben die Hersteller von Lautsprecherstativen ein grundlegendes Problem: Sie wissen nicht, wie hoch eure Boxen an genau eurem Arbeitsplatz stehen (müssen). Es gibt zwar kommerziell erhältliche Ständer mit einer festen Bauhöhe, aber die passen halt eher zufällig. Abhilfe schaffen Ständer, die sich in der Höhe verstellen lassen, aber das hat ein neues Problem zur Folge: Damit solche Ständer trotz der Höhenverstellung ausreichend stabil sind und nicht mitschwingen, bedarf es recht massiver und ausgefuchster Verstell-Mechanismen – was sich dann wieder im Preis widerspiegelt.
Der Do-It-Yourself-Vorteil
Als Selbstbauer haben wir also einen klaren Vorteil: Wir brauchen nur ein Maßband, um unsere perfekte Stativhöhe auszumessen und können uns die komplizierte Höhenverstellung sparen. Das erlaubt uns, einfache, aber sehr stabile und schwingungsarme Ständer zu bauen, maßgeschneidert auf unsere Anforderungen. Mit etwas handwerklichem Geschick, Geduld und Spucke müssen sich die DIY-Ständer auch nicht vor den kommerziellen Kollegen verstecken. Außerdem macht das Basteln ja Spaß und es erfüllt einen mit einer gewissen Befriedigung, wenn die teuren Boxen auf den selbstgebauten Ständer im Studio stehen.
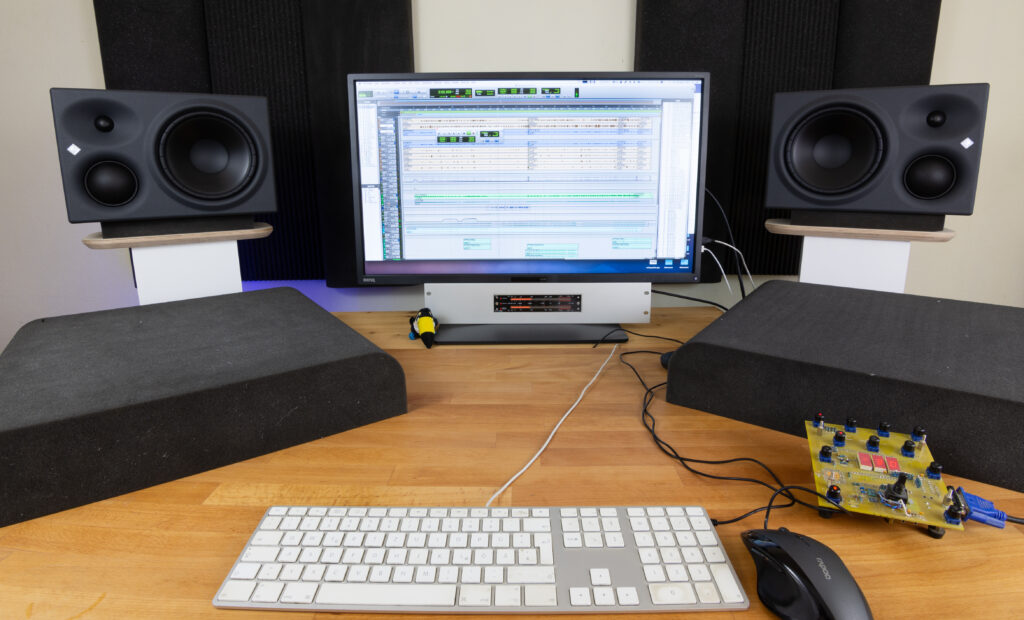
DIY-LAUTSPRECHERSTÄNDER: PLANUNG
Anforderungen an die Selbstbau-Stative
Genug der Theorie, was bauen wir jetzt genau? Nun: Zwei Boxenständer, die folgende Anforderungen erfüllen sollen:
- Sie sollen die Studio-Monitore, bzw. das akustische Zentrum der Box auf die richtige Höhe (Ohrhöhe am Arbeitsplatz) bringen.
- Sie sollen so stabil gebaut sein, dass nichts mitschwingt und auch keine Schwingungen an den Arbeitstisch, die Meterbridge oder den Studioboden übertragen werden. Dazu sollen sie Säulen mit Sand befüllt werden können.
- Der Bau soll einfach und ohne großes Spezialwerkzeug möglich sein.
- Die Ständer sollen zerlegbar sein (falls mal ein Umzug ansteht).
- Wenn möglich, sollen die Netz- und Audio-Kabel außer Sicht verlegt/aufgeräumt werden können.
- Die Ständer sollen optisch ein bisschen was hermachen, zum Beispiel sollen von außen keine Schrauben zu sehen sein.
Diese DIY-Stative, andere DIY-Stative
Wichtige Anmerkung, bevor es los geht: Die hier beschriebenen Ständer habe ich nach meinen Bedürfnissen und mit den mir zur Verfügung stehenden Mitteln gebaut. Das wird sich nicht eins-zu-eins mit euren Anforderungen decken (Bauhöhe der Stative, verfügbares Werkzeug, etc.). Aber auf der Basis der hier beschriebenen Konstruktion könnt ihr euch „eure“ Ständer ausdenken und bauen, wenn nötig versuche ich immer eine Alternativ-Lösung zu meiner Bauweise anzubieten.
Schritt 1: Höhe bestimmen
Der erste Schritt zum eigenen DIY-Lautsprecherstativ ist also eine Messung: Wir müssen die korrekte Höhe der Box bestimmt. Ich gehe jetzt mal davon aus, dass eure Lautsprecher schon im richtigen Abstand und im richtigen Winkel ausgerichtet sind. Wer hier noch unsicher ist, kann das in unserem Workshop zur Aufstellung von Studio-Monitoren nachlesen. Generell sagt man, dass der Hochtöner der Box auf der Höhe unserer Ohren abstrahlen soll. Besser und noch genauer wird es, wenn man das „akustisches Zentrum“ seiner Box kennt. Diese Angabe liefern viele, aber leider nicht alle Boxen-Hersteller in den Spezifikationen oder Manuals. Bei meinen Neumann KH310 steht zum Beispiel in der Anleitung, dass das akustische Zentrum der Box genau zwischen Hoch- und Mitteltöner liegt, dieser Punkt muss also am Ende auf Ohrhöhe am Arbeitsplatz liegen.

Die Bauhöhe der DIY-Stative
Von diesem eben gemessenen Wert ziehen wir den Abstand des akustischen Zentrums bis zur Unterkante der Box ab – und voilà: Wir haben die angestrebte Bauhöhe unserer DIY-Ständer bestimmt! Wer plant, die Boxen auf Spikes oder eine Schaumstoffunterlage zu stellen, sollte diesen Wert noch von der Gesamthöhe abziehen. Eine Beispielrechnung für meinen Fall: Das akustische Zentrum soll auf etwa 116 cm liegen. Der Abstand von diesem Punkt zur Unterkante der Box beträgt 13 cm. 116 cm – 13 cm = 103 cm Bauhöhe der Stative. Um eventuell noch etwas Spielraum mit Boxenunterlagen wie Schaumstoff oder Spikes zu haben, ziehe ich weitere vier Zentimeter ab und komme auf eine Gesamthöhe von 999 Zentimetern. So hoch solle am Ende mein Stativ also sein. Unter uns: Auf den Millimeter kommt es hier nicht an, plus/minus einen Zentimeter Abweichung geht in Ordnung.
Gibt es eine maximale Bauhöhe?
So ein Säulenständer wird ab einer gewissen Höhe instabil. Der Schwerpunkt wandert bisweilen so hoch, dass die Ständer wieder zu der wackeligen Angelegenheit werden, die wir eigentlich vermeiden wollten. Dem kann man mit größeren Abmessungen zum Beispiel des Standfußes oder der tragenden Säule ein bisschen entgegenwirken, aber irgendwann wird es einfach zu hoch. Die hier beschriebenen DIY-Ständer sind für Lautsprecher im Nahfeld gedacht, wobei sich die Stativhöhe in der Praxis im Rahmen von 90 cm bis 1,2 Metern bewegen dürfte. Benötigt ihr einen deutlich höheren Aufbau, ist eine Abhängung der Boxen von der Decke eventuell die bessere Lösung.
Schritt 2: Die 5-Minuten-Konstruktion
Im Prinzip ist die Konstruktion der Boxenständer in fünf Minuten erledigt, wir brauchen lediglich drei einfache Teile: eine Bodenplatte, eine rechteckige tragende Säule und eine Abstellplatte für die Boxen. Und dann noch eine Lösung, wie wir diese drei Teile fest miteinander verbinden können.
Bleistift oder CAD-Programm?
Bevor der Leim gezückt wird, wird eine Zeichnung des Ständers erstellt. Eine einfache Bleistiftskizze mit den Maßangaben reicht aus. Noch genauer wird es, wenn man ein CAD-Programm verwendet. Es gibt sehr viele leistungsstarke CAD-Programme, allen voran Autodesk Fusion 360, welches man als Hobbyanwender (Stand 2021) für ein Jahr kostenlos nutzen kann. Daneben gibt es jede Menge weiterer CAD-Freeware-Programme: Zum Beispiel „FreeCAD“, das für Windows, Mac und Linux erhältlich ist, oder die kostenlosen Basic-Version von „SketchUp“. Für die hier gezeigte Stativ-Konstruktion reichen eigentlich alle Freeware-CAD-Programme völlig aus!
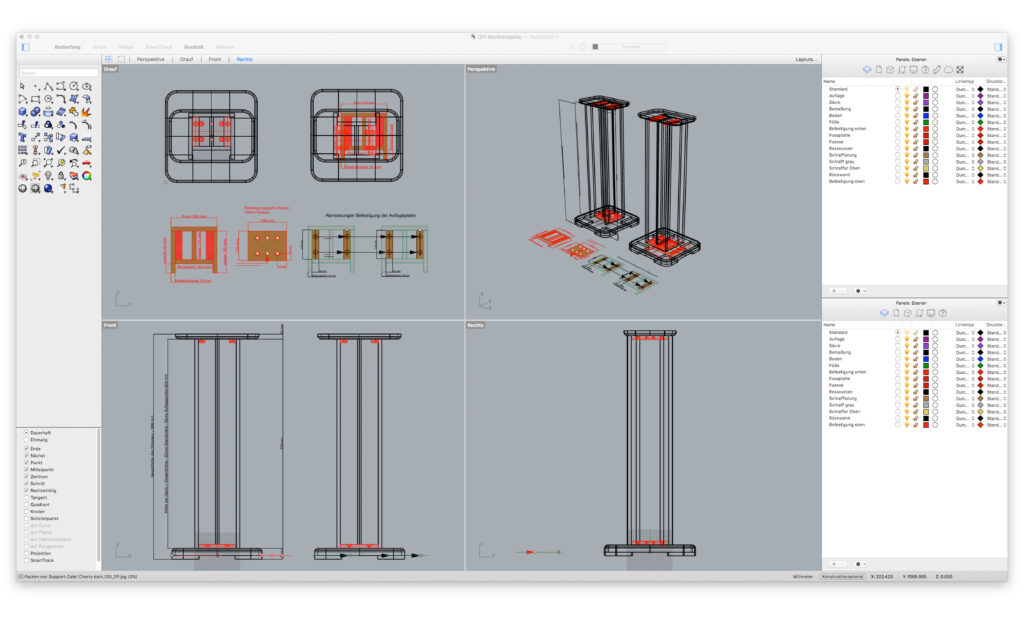
Teil 1: Die Bodenplatte
Wie benötigen eine stabile Bodenplatte. Je höher der Ständer ist, desto größer sollte die Grundfläche dieser Bodenplatte sein. Die Abmessung hängt aber auch vom vorhandenen Platz am Standort der Ständer ab. Wichtig ist nur, dass die Bodenplatte ausreichend groß ist, damit das Stativ am Ende sicher steht. Eigentlich wäre eine dreieckige Grundplatte die bessere Wahl (da beim Dreieck nichts wackelt), die Dreieckesform erschwert aber den Zuschnitt der Bodenplatte enorm. Alle Baumärkte (in meiner Umgebung) schneiden nur im rechten Winkel zu. Deshalb wähle ich für den DIY-Ständer eine quadratische Form. Falls ihr die Möglichkeit, habt euch die Bodenplatte im 60° Grad Winkel zuschneiden zu lassen (oder selbst die Säge schwingt), spricht nichts gegen eine dreieckige Bodenplatte.
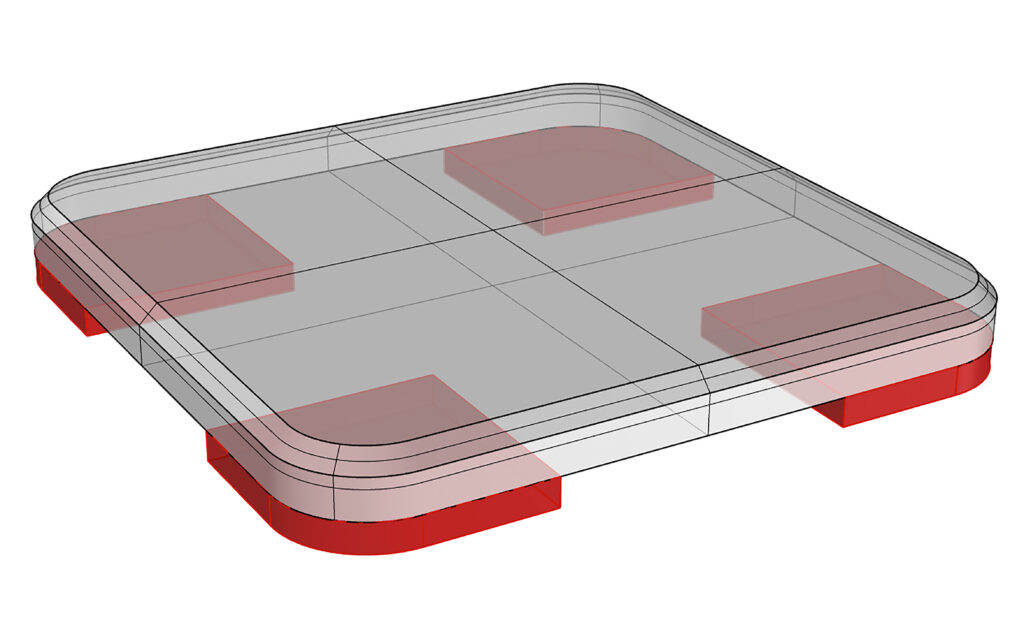
Die tragende Säule
Die Säule besteht aus vier Platten, die verleimt oder verschraubt werden. Die Grundfläche dieser Säule sollte nicht zu groß sein, aber dennoch groß genug, damit später alles stabil steht. Die Höhe der Säule ergibt sich aus der gewünschten Gesamthöhe der Ständer, abzüglich der Dicke der Boden- und Auflageplatte. Ich habe als zusätzlichen Versteifung der Säule einen Innenstrebe eingeplant, deshalb besteht meine Säule aus fünf Platten.
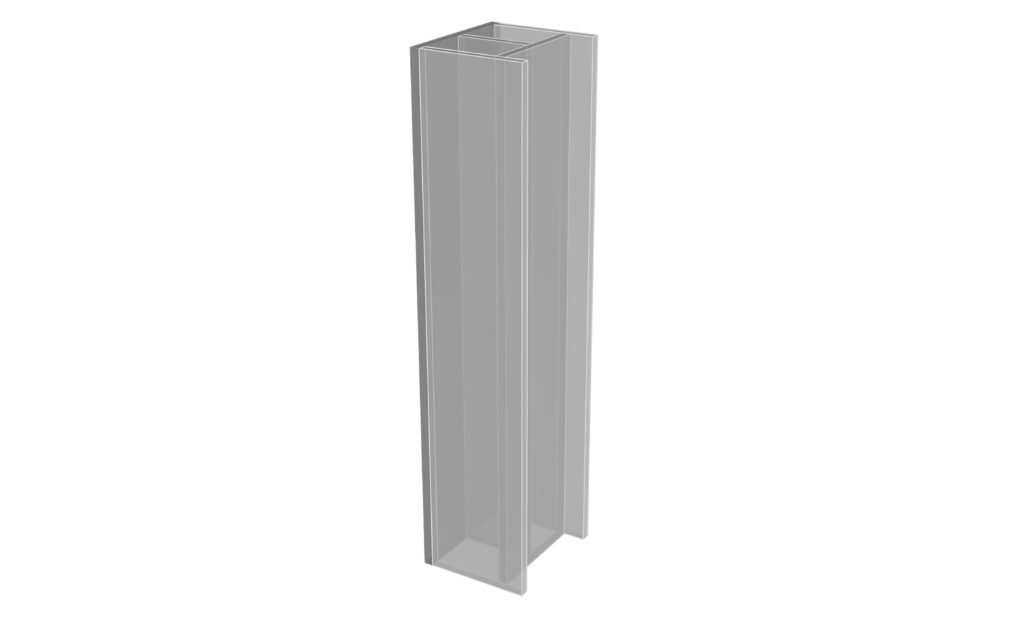
Die Abstellplatte
Die Abstell- oder Auflageplatte, auf der die Boxen später stehen, bietet uns die Möglichkeit der ultimativen Maßanfertigung! Hier kann man so angepasst auf die eigenen Abhörmonitore bauen, wie es den kommerziellen Herstellern nicht möglich ist! Die Abmessung für eure Auflageplatte könnt (und müsst) ihr selbst bestimmen. Ich persönlich finde es schöner, wenn die Bodenplatte nicht größer als die Grundfläche der Box selbst ist, aber das muss ja nicht euer Geschmack sein! Wichtig ist nur, dass die Auflageplatte groß genug ist, damit der Lautsprecher sicher darauf steht.

Die Verbindungsplatten
Die Bodenplatte, die Säule und die Auflageplatte müssen fest miteinander verbunden werden, und diese Verbindung soll später lösbar sein. Dieser Part ist der komplexeste der ganzen Stativkonstruktion, die Lösung ist dennoch einfach und billig: zusätzliche Verbindungsstück für die Boden- und Auflageplatte, in die Einschlagmuttern eingelassen werden. Einschlagmuttern sind Muttern mit vier Metallzacken und einem Innengewinde aus Metall. Durch das Anziehen der Schrauben zieht sich die Einschlagmutter ins Holz und sorgt für eine feste Verbindung. Durch das Metallgewindes kann die Verschraubung beliebig oft gelöst und wieder angezogen werden. Als Schrauben kann man Zylinderkopfschrauben mit flachen Schraubenköpfen und Innensechskant verwenden. Zylinderkopfschrauben und Einschlagmuttern findet man sehr günstig in der Hardware-Abteilung im Baumarkt.
SELBSTBAU-STATIVE: BAUPHASE
So, jetzt wird es langsam konkret: Im Folgenden beschreibe ich, wie ich „meine“ DIY-Monitorständer gebaut habe. Sicherlich nicht der Weisheit letzter Schluss, aber sie tun – soviel sei verraten – seit einiger Zeit gute Dienste. Kritik oder Verbesserungsvorschläge sind willkommen, dazu bietet bondeo eine Kommentarfunktion unter dem Artikel. Genauso wie der Ständer in fünf Minuten konstruiert ist, kann man ihn auch in fünf Minuten zusammenschustern. Funktional wäre das kein Problem, optisch allerdings schon! Deshalb habe ich mir etwas Mühe gegeben, damit das Endergebnis halbwegs vorzeigbar ist. Die Arbeitsschritte, die der reinen Optik dienen, könnt ihr auch weglassen – oder um weitere Verschönerungen ergänzen (zB LED-Strips). Der CAD-Zeichnung entnehme ich alle benötigten Maße für den Zuschnitt des Materials, ganz nebenbei kann man sich schon mal ein grobes Bild machen, wie die Stative später aussehen werden.
Schritt 3: Das Material besorgen
Das geeignete Material für den Bau der DIY-Stative ist die „mitteldichte Faserplatte“, kurz MDF-Platte genannt. Bei der Herstellung der MDF-Platten werden fein Holzfasern mit einem Bindemittel unter hohem Druck verpresst. In der Verarbeitung ist MDF kein angenehmer (eher ein furchtbarer) Werkstoff, und schön sieht das schlammbraune Zeugs auch nicht aus. Es stellt sich also die berechtigte Frage, warum wir dennoch MDF verwenden und nicht Leimholz, oder Multiplex-, bzw. Sperrholzplatten? Trotz aller Nachteile hat MDF ein paar Vorteile, die es für die Anwendung „Boxen-Ständer“ zum idealen Material machen: Zum einen ist es preiswert, für meine beiden Stative habe ich inklusive Zuschnitt etwa 40 Euro bezahlt. MDF lässt sich außerdem leicht sägen, verschrauben und verleimen und anders als Massivholz oder Multiplex-Platten verzieht sich MDF später nicht mehr. Die homogene „Konsistenz“ der verpressten Fasern sorgt dafür, dass die Platten kaum zum Schwingen neigen, weshalb viele Lautsprechergehäuse – selbst die von hochpreisigen Exemplaren – aus MDF bestehen. Letztlich ist es also kein schönes, aber ein geeignetes Material für unsere Stative. Lediglich für die Auflageplatte habe ich Multiplexplatten verwendet, hier allerdings aus rein optischen Gründen.
Mit der Schnittliste in den Baumarkt
Wer eine Hand- oder Tischkreissäge besitzt, kann den Zuschnitt der MDF-Platten selbst erledigen, aber einfacher und im Zweifelsfalle genauer ist der Zuschnitt im Baumarkt. Ihr benötigt für die zwei Stative hier gezeigten Stative folgende Materialien:
- MDF 16 mm, 400 x 400 mm, vier Stück (Bodenplatte)
- *MDF 16 mm, 140 x 140, acht Stück (Füße der Bodenplatte)
- Alternativ: MDF 16 mm, 280 x 280, zwei Stück (Füße, Zuschnitt mit der Hand)
- MDF 16 mm, 929 x 200 mm, zwei Stück (Frontplatte)MDF 16 mm, 929 x 184 mm, vier Stück (Seitenplatten)
- MDF 16 mm, 929 x 168 mm, zwei Stück (Rückwand)
- MDF 16 mm, 914 x 128 mm, zwei Stück (Innenstrebe, Achtung: die Länge ist abhängig von der Dicke der unteren Befestigungsplatte)
- Multiplex 22 mm, 370 x 230 mm, zwei Stück (Auflageplatte, die genaue Abmessung ist abhängig von euren Lautsprechern!)
- *Multiplex 15 mm, 168 x 128 mm, zwei Stück (Befestigungsplatte unten)
- Alternativ: Multiplex 15 mm, 168 x 256 mm, ein Stück (Zuschnitt mit der Hand)
- ein Kantholz aus Buche oder Eiche (Hartholz), 30 x 30 mm, gibt es in Meterstücken
*Achtung: Mindestgrößen im Zuschnitt!
Alle Baumärkte weisen für den Zuschnitts-Service eine Mindestgröße aus, unter der nicht mehr gesägt wird (die Maße können je nach Markt unterschiedlich ausfallen). Die mit einem Stern gekennzeichneten Teile fallen vermutlich unter diese Grenze, müssen also selbst zugeschnitten werden. Bei den Füßen kann man sich zum Beispiel eine 280 x 280 mm große Platte besorgen und diese in vier Vierecke auftrennen. Bei der unteren Befestigungsplatte geht das auch: Anstatt zwei einzelnen 168 x 128 mm großen Teilen, wird ein 168 x 256 mm großes Stück besorgt, das man dann in der Mitte durchsägt. Somit sind zumindest drei der vier Seiten 100% im rechten Winkel, wenn eine Seite später nicht perfekt passt, ist das nicht so schlimm. Kleine Motivationshilfe am Rande: Nichts an diesem DIY-Stativ muss, aber alles darf perfekt sein!
Ihr benötigt für den Bau noch ein paar Dinge, solange der Kollege beim Zuschnitt eure Platten sägt, könnt ihr den Einkaufswagen mit folgenden Dingen füllen:
- Eine mittelgroße Flasche (225g) Holzleim (egal welcher…)
- Schleifpapier in der Körnung 80, 120, 240, je ein Bogen
- 16 Einschlagmuttern M6 x 9
- 16 Zylinderkopfschrauben M6 x 50, mit Innensechskant und flachem Kopf
- 16 Federringe M6
- 16 Unterlegscheiben 6,4 x 18 mm
- min. 28 kleine Stuhlwinkel 40 x 40 mm
- Spannplattenschrauben, je ein Päckchen 3×16, 4×25, 4×40
- 2 x 25 kg Quarzsand (oder Filtersand aus der Pool-Abteilung)
Wer die Säulen später noch lackieren möchte, benötigt dafür zusätzlich:
- MDF-Grundierung oder Acryl-Multigrund, 750 ml-Dose
- Acryllack für den Innenbereich in der Wunschfarbe, 375 ml
- Lackierrollen aus Schaumstoff (sind besser als Pinsel…) und eine kleine Farbwanne
- 120er und 240er Schleifpapier, für den Zwischenschliff
Für den Bau benötigt ihr folgendes Werkzeug:
- persönliche Schutzausrüstung: Gehörschutz, Schutzbrille, Staub-, bzw. Atemschutzmaske
- Maßstab oder Maßband 2 m
- kleinen Schreiner- oder Anschlagswinkel mit 90° Grad, oder mehrere „Verleimhilfen“ (siehe Text)
- Zwingen (möglichst viele), ein dickes Seil oder Gewichte zum Verleimen
- Akkuschrauber
- Holzbohrer, Größe 7 oder 8 mm
- Innensechskantschlüssel 4 mm
- Torx-Bit T10 und T15 oder passende Schraubendreher (für die Spannplattenschrauben)
Grundsätzliches zur Verleimung der DIY-Ständer
Ich habe meine DIY-Stative mit so genannten „Lamellos“ (Größe 10) verleimt, das sind flache Holzdübel, die in speziell gefräste Nuten eingeleimt werden. Allerdings benötigt man dafür eine Flachdübelfräse (ein eher spezielles Werkzeug aus dem Möbelbau), welche nicht zur Standardausrüstung eines Hobbybastlers gehört. Wer aber Zugriff auf eine solche Fräse hat: Go for it! Es macht das Verleimen der MDF-Platten sehr einfach.
Sichere Verbindung mit Stuhlwinkeln
Allen anderen empfehle ich eine Kombination aus Holzleim und von innen angeschraubte Stuhlwinkeln, wie es bonedo-Autor Felix Klostermann im DIY-Workshop zu den Seitenabsorbern schon gezeigt hat. Vor allem die untere Befestigungsplatte solltet ihr mit solchen Stuhlwinkeln festschrauben (weil hier die größten Kräfte wirken). Ihr benötigt pro Stativ etwa 14 bis 22 Stuhlwinkel (sechs für die Befestigungsplatte, acht Stück zum Verbinden der Platten, weitere acht zum Verschrauben der Innenstrebe). Insgesamt also mindestens 28 Stück, für zwei Stative. Festgeschraubt werden die Winkel mit 3x16er Spannplattenschrauben.
Schritt 4: Verleimen der Bodenplatten
Die Bodenplatte besteht aus zwei 400 x 400 x 16 großen MDF-Platten, die flächig verleimt werden. Damit sich die beiden Platten beim Verleimen nicht verschieben, könnt ihr einfach etwas grobes Kochsalz auf die Leimfläche streuen. Zum Beschweren taugen die beiden 25 kg-Säcke mit Quarzsand, mit denen später die Säule befüllt wird. Da normaler Weißleim (bzw. Holzleim) schon nach wenigen Minuten abgebunden ist, kann man nach ca. 30 bis 60 Minuten (je nach Raumtemperatur) die Platten von den Zulagen befreien und weiterarbeiten. Die vier Standfüße werden angeleimt und mit Schrauben (4×25) fixiert. Zuletzt werden die Löcher für die Verschraubung mit der Säule angezeichnet und mit einem 7mm-Holzbohrer durchgebohrt. Die Löcher sind mit sieben Millimeter etwa einen Millimeter größer als nötig. So hat man später Spielraum beim Verschrauben, falls nicht alle Bohrungen exakt sitzen. Auf meinen Fotos seht ihr noch Sacklöcher, in denen die Schraubenköpfe verschwinden, das gehört zu den (optionalen) optischen Arbeiten, die könnt ihr also auch weglassen. Ach ja: Gratulation: Damit ist der erste Teil des DIY-Stativs schon fertig!
Schritt 5: Herstellung der Befestigungsstücke
Die Bodenplatte soll später mit der Säule verschraubt werden. Dazu dient eine 15 mm dicke Multiplex-Platte, in die vier Einschlagmuttern eingelassen werden. Man sollte hier möglichst genau arbeiten, da diese Verbindung die größten Kräfte am Stativ aushalten muss. Die Bohrungen werden angezeichnet und wieder mit dem 7er Holzbohrer (für etwas Spielraum) durchgebohrt. Diese Löcher sollten möglichst gerade durchs Material gehen, beim Bohren mit der Hand hilft ein Anschlagswinkel zur Ausrichtung des Akkuschraubers. Als zusätzliche Verstärkung habe ich die Bodenplatte mit zwei 4x40er Spannplattenschrauben an der Innenstrebe befestigt.
Die obere Auflageplatte wird ebenfalls mit Einschlagmuttern befestigt, allerdings genügen hier kurze rechteckige Kanthölzer, die innen an der Säule angeleimt werden und zusätzlich mit zwei Spannplattenschrauben (ca. 4×40) gesichert werden. Diese Verbindung wird später kaum belastet, ich habe trotzdem hartes Buchenholz verwendet. Bei weichem Fichtenholz besteht die Gefahr, dass das Holz durch die Zacken der Einschlagmutter splittert. Die Löcher wurden an der Standbohrmaschine gebohrt und die Muttern mit Hilfe einer Schraube vormontiert und schon mal fest ins Holz gezogen.
Schritt 6: Verleimen der MDF-Säule
Das Verleimen der fünf MDF-Platten zur tragenden Stativsäule geschieht in drei Schritten: Im ersten Schritt werden die Seitenteile und die Rückwand zusammen mit der unteren Befestigungsplatte verleimt. Sobald der Leim hier trocken ist, kann – Verleimschritt zwei – die Innenstrebe eingeleimt werden. Ganz wichtig: Die untere Befestigungsplatte muss spätestens jetzt mit den Stuhlwinkeln angeschraubt werden (siehe Bild im Abschnitt: „Sichere Verbindung mit Stuhlwinkeln“)! Ihr könnt die untere Platte auch nur an den Seitenwänden, der Rückwand und der Innenstrebe anschrauben. Sobald die Frontplatte aufgeleimt ist, ist die untere Befestigungsplatte unerreichbar (zugegeben: Das ist ein kleiner Konstruktionsfehler). Wem das alles zu viel Aufwand ist, kann von außen Schrauben durch das MDF in die Kante der Multiplexplatte jagen (dann aber bitte vorbohren!). Das hält bombenfest, aber es sieht halt nicht so schön aus. Beim Verleimen von rechtwinkligen Konstruktionen wie unserer Säule, sind kleine Holzwinkel, sogenannte „Verleimhilfen“ extrem hilfreich. Im Netz findet man dazu jede Menge Bauanleitungen und solche Teile sind schnell aus Reststücken gebastelt. Zum Abschluss wird – Verleimschritt drei – die Frontplatte angebracht und die Säule ist somit fertig! Da der Leim schnell abbindet, muss man zügig arbeiten, deswegen habe ich kaum Fotos von den Verleimschritten. Das berühmte „Zwingenbild“ darf aber in keinem DIY-Artikel fehlen! Apropos Zwingen: Wer nicht genug Zwingen besitzt, kann sich mit allem behelfen, was schwer genug ist, die Platten zusammenzudrücken. Selbst ein starkes Seil, dass man stramm um die Säule wickelt, kann hier helfen. Das sichtbare Zeichen einer guten Verleimung ist Leim, der aus den Fugen quillt!
Zwischenstand
Wenn ihr soweit gekommen seid, habt ihr im Prinzip schon einen funktionierenden Ständer gebaut. Ihr müsstet nur die Bodenplatte und die Auflageplatte an die Säule anschrauben, den Sand reinfüllen und wärt fertig! Die genauen Positionen der Löcher für die Verschraubung habe ich euch nochmal in zwei Grafiken zusammengefasst. Ein kleiner Trick zum Anzeichnen der Löcher: Mit spitzen Dübelmarkierern kann man die Position von Schraublöchern super genau und komplett ohne Messmittel markieren (ich habe das bei der Auflageplatte gemacht): Die Platte wird an der Wunschposition ausgerichtet und dann angedrückt. Dabei bohren die Spitzen kleine Löcher ins Material, die gleich als Führung für den Holzbohrer dienen.
Schritt 7: Schöner machen!
Der Boden- und der Auflageplatte rücke mit der Oberfräse zu Leibe: Die Ecken werden abgerundet und ich bringe eine 45°-Fase an der Oberkante der Bodenplatte und der Unterkante der Auflageplatte an. Dadurch wirken diese Platten nicht so massiv und es gibt keine Ecken, an denen man sich schmerzhaft stoßen kann. Die Oberkante der Bodenplatte und die Unterkante der Auflageplatte werden ebenfalls mit einer 45° Grad Fase versehen. Hier kommt wieder die Oberfräse zum Einsatz, diesmal mit einem Fasenfräser. Bei solchen Arbeiten ist die persönliche Schutzausrüstung Pflicht: Dazu gehören ein Gehörschutz, die Schutzbrille und die Atemschutzmaske!
Schritt 8: Grundieren und Lackieren
Wollt ihr die DIY-Stative farbig lackieren, müsst ihr auf jeden Fall vorher eine Grundierung auftragen. Das MDF ist vor allem an den Kanten saugfähig wie ein Schwamm, ohne Grundierung wird der Lack tief ins Material hineingezogen, was später unschön aussieht. Es gibt viele Arten, wie man MDF-Kanten versiegeln kann, für die Kanten habeZweikomponenten-Spachtelmasse aus dem Automobilbedarf verwendet (eine kleine Dose mit 245g Spachtelmaße reicht für beiden Stative aus). Das Zeugs riecht leider streng nach „Chemie“, wenn es geht sollte man an der frischen Luft spachteln, ansonsten eine Atemmaske tragen und für gute Belüftung sorgen! Ist die Spachtelmasse durchgetrocknet, werden die Kanten mit Schleifpapier (120er Körnung) glattgeschliffen.
Dann geht es an die Grundierung der Oberflächen mit speziellem Acrylgrund, der mit der Lackrolle dünn aufgetragen und nach dem Trocknen mit immer feinerem Schleifpapier zwischengeschliffen wird. Diesen Vorgang wiederhole ich drei Mal, den letzten Schliff vor dem Lackieren habe ich mit 240er Schleifpapier erledigt. Hat man gewissenhaft grundiert, reichen später zwei Schichten Lack für eine schöne farbige Oberfläche aus (wiederum mit einem Zwischenschliff mit 240er Schleifpapier). Meine Stative habe ich mit weißen Acryllack für Innenräume bepinselt. Wer es individueller mag, kann Schultafellack verwenden und die Stative später mit Malkreide verschönern, oder von den Musikern und Kunden verschönern lassen! Leider kam mir die Idee mit dem Tafellack zu spät, aber vielleicht hole ich das noch nach.
Schritt 9: Das Befüllen mit Quarzsand
Bevor die fertigen DIY-Stative ihrer Bestimmung übergeben werden, werden sie zur Erhöhung der Masse und der Stabilität mit Quarzsand befüllt. Hier kommt ein bisschen CAD-Magie ins Spiel, den die Frage nach der benötigten Sandmenge liefert uns eine simple Volumenberechnung unserer „Säulen“. Laut CAD-Programm hat jede Säule ein Volumen von 0,02 m3. Mit dieser Angabe und einem Baustoffrechner im Internet komme ich auf eine benötigte Menge an Quarzsand von 30 kg pro Säule, für die komplette Befüllung eines Hohlraums. Da mein Baumarkt den Quarzsand in zehn oder 25 kg-Säcken führt, packe ich mir zwei 25 kg Säcke auf den Wagen, das sollte reichen, bzw. kann ich ja jederzeit Nachfüllen oder wieder Sand entnehmen. Ich habe übrigens den (etwas teureren) Sand für Poolfilter verwendet, weil der als „getrocknet“ und vor allem als „geruchsneutral“ beworben wurde.
Was hat der ganze Spaß gekostet?
Ob man bei so einem DIY-Projekt am Ende tatsächlich Geld spart, ist immer eine schwierige Frage. Nimmt man die eigene Arbeitszeit in die Rechnung mit auf, ist fast immer das Gegenteil der Fall. Meine beiden hier gezeigten Stative schlagen mit etwa 110 Euro an reinen Materialkosten zu Buche, die Kosten für die vergleichsweise teuren Lackierung (inklusive Spachtelmasse) sind hier mit eingerechnet. Ohne Lackierung liegen die Kosten mit den 50 kg Quarzsand für die Befüllung bei etwa 80 Euro für zwei Ständer. Und wer einen eigenen Sandkasten plündern kann: Die reinen Materialkosten für den Zuschnitt und die Schrauben-Hardware liegt bei etwa 65 Euro für zwei Stative.
Diggnity sagt:
#1 - 20.05.2022 um 15:36 Uhr
Interessanter Artikel und schöne Lösung. Abschließend bleibt bei mir aber die Frage offen, ob die Vibrationen der Boxen jetzt minimiert wurde bzw. aufgrund der Masse vollständig eliminiert sind oder nicht? Statt innerhalb der Säule die Winkel zu verwenden (bin da kein Freund von Winkeln) wäre es auch möglich mit der Oberfräse längliche Nuten mit 1/3 Tiefe der Brett-Dicke in die Säulenbretter zu sägen und dann ordentlich zu verleimen. Das sollte die Stabilität auch noch mal um einiges erhöhen. Um den richtigen Anpressdruck zu schaffen, können auch Spanngurte verwendet werden, wenn die Ecken und die Auflage der Metallteile mit Pappe geschützt werden - wer hat schon sooo viele passende Zwingen rumliegen... Verbesserungen für die MK II: Höhenverstellung, falls man doch mal umzieht oder den Schreibtisch wechselt Unter der Bodenplatte etwas rutschfestes, elastisches Material befestigen oder höhenverstellbare Spikes aus dem Hifi-Gewerbe verwenden.
Rico sagt:
#2 - 29.11.2022 um 20:55 Uhr
Ein heißer tip ist mittels Abklopfen mit einem Gummihammer die Sanddichte nochmals deutlich zu erhöhen, Ihr werdet euch wundern wie viel da noch absackt. Das erhöt den Dämpfungsfaktor tiefer Frequenzen enorm und führt zu einen noch stabileren Bass bzw. Grundtonverhalten.
Manfred sagt:
#3 - 13.02.2024 um 07:44 Uhr
Ich habe meine DIY Boxenständer mit Sand gefüllt um Vibrationen zu verhindern. Meine Boxenständer haben nur drei Füße, den drei Füße können nicht kippeln, ausserdem sind die Füße nevillierbar um sie in Waage ausrichten zu können.